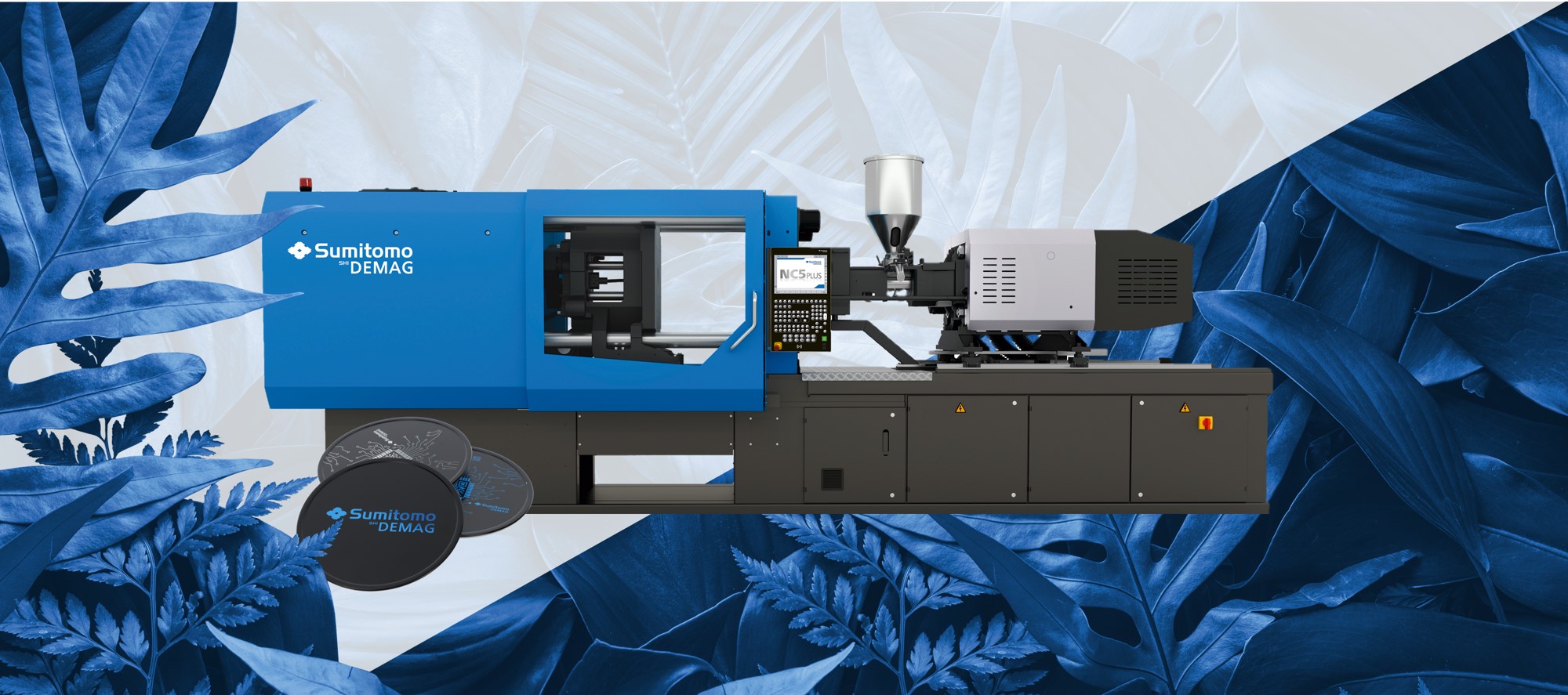
Sustainable towards the future of mobility
Modular wallbox cover production
We showcase our in-mould decoration (IMD) process expertise, manufacturing a complex electric vehicle (EV) application on an all-electric IntElect 220/660-1100 injection moulding machine. Creating a smart e-charging Wallbox cover, weighing 110 grams, in a 60 second cycle time, this new demonstration centres around sustainability. Despite its decor and complexity, the manufactured IMD part is especially durable due to its special material properties. Yet, the fully recyclable material used - a Makrolon RE polycarbonate supplied by Covestro - is also CO2-neutral.
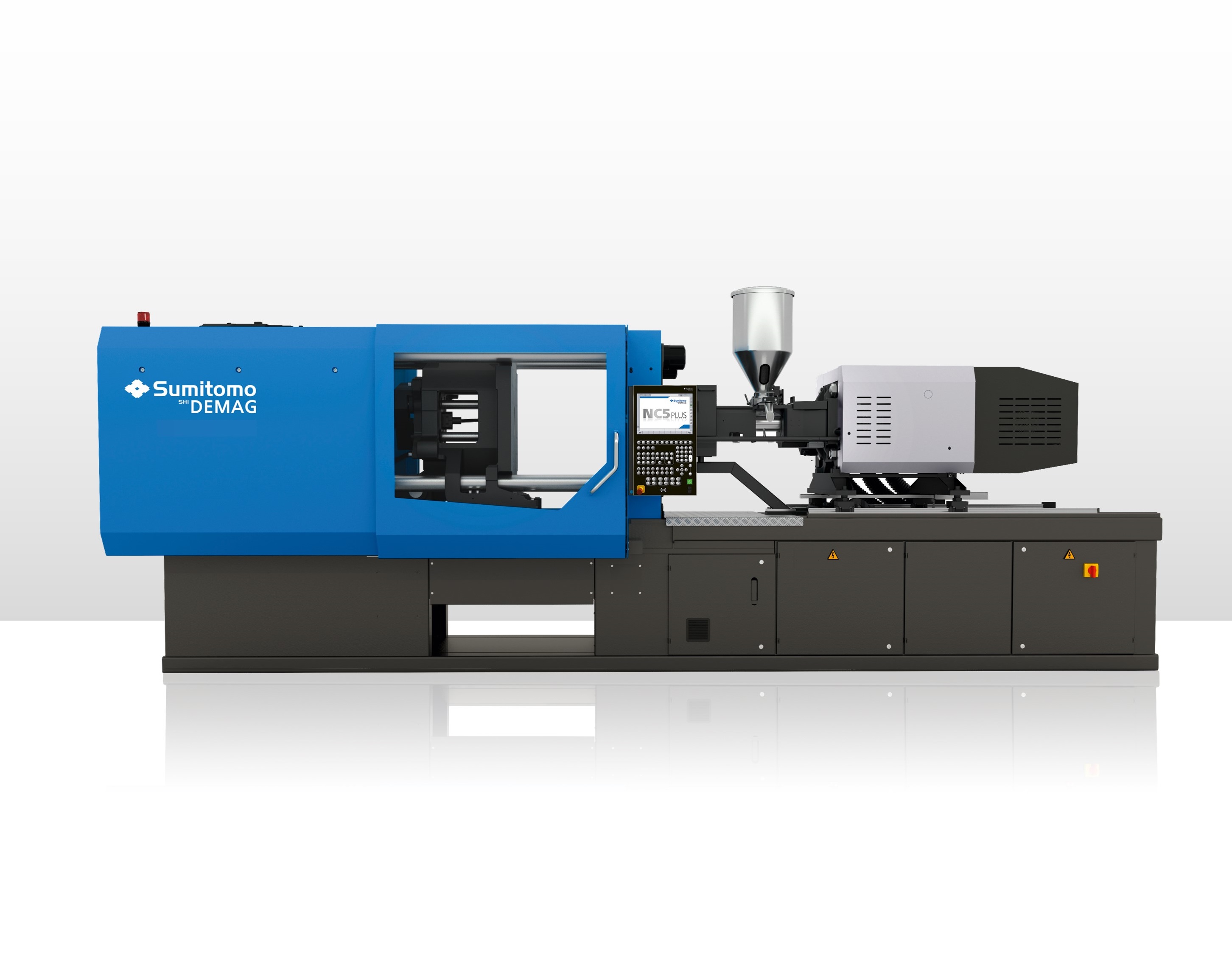
K 2022 modular IMD application
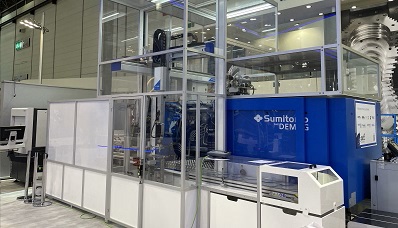
- Energy efficient
- Highly precise
- Dynamic
- Clean production cell
- Robot: SD 22x
- Gate cutting system from Frimo
- Laser system from ACSys
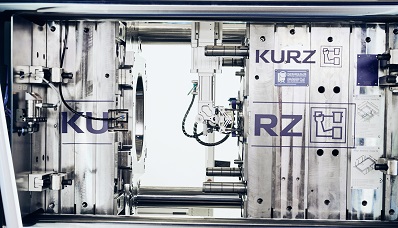
- 1 Kavität
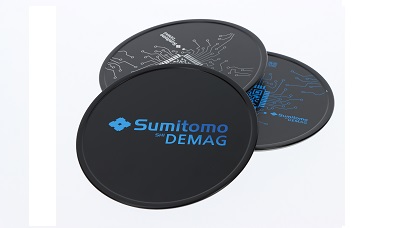
- Part weight: 110g
- Part fully recyclable
- PC Makrolon 6557RE
-
Multiple decoration options in one production cell
- IMD (personalizable via laser technology, as shown on our booth)
- IML (seperate process, possible on the same machine)
- Hot stamping (seperate process)
- Digital print (seperate process)
- Functional foil bonding (seperate process)
We are showing a flexibly expandable and thus cost-efficient production solution, with the core of an extremely energy-efficient and precise all-electric injection moulding machine.
Rustam Aliyev, Director Business Development Automotive